Intro
Unlock the secrets of Lockheed Martins 3D printing innovation with this in-depth article. Discover 5 key insights into the additive manufacturing process used to produce the F-35 fighter jets engine components, including design optimization, material selection, and reduced production time. Dive into the world of 3D printing in aerospace and explore its transformative impact.
The world of 3D printing has been rapidly evolving, and one of the most significant areas of innovation is in the field of aerospace engineering. Lockheed Martin, a leading player in the aerospace industry, has been at the forefront of 3D printing technology, using it to create complex engine components. In this article, we will delve into the world of 3D printing Lockheed engines, exploring five key insights that highlight the benefits, challenges, and future directions of this technology.
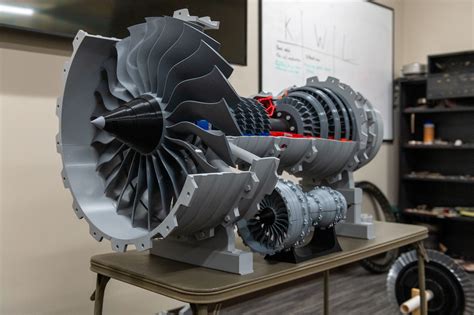
Advantages of 3D Printing in Aerospace Engineering
The use of 3D printing in aerospace engineering offers several advantages, including reduced production time, increased complexity, and lower costs. Traditional manufacturing methods often involve multiple steps, such as casting, machining, and assembly, which can be time-consuming and expensive. In contrast, 3D printing allows for the creation of complex geometries and structures in a single step, reducing production time and costs.
Key Insights into 3D Printing Lockheed Engines
1. Increased Complexity and Customization
One of the primary benefits of 3D printing is the ability to create complex geometries and structures that would be impossible to produce using traditional manufacturing methods. Lockheed Martin has leveraged this capability to create customized engine components with complex internal structures, such as cooling channels and fuel injectors.
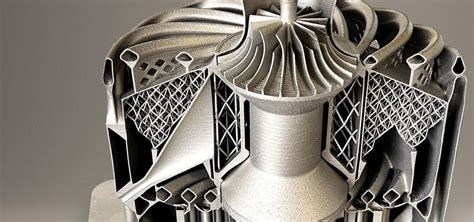
2. Reduced Weight and Improved Performance
The use of 3D printing in aerospace engineering also enables the creation of lightweight components with improved performance. By optimizing the internal structure of engine components, Lockheed Martin has been able to reduce weight while maintaining or improving performance. This is critical in aerospace applications, where weight reduction can lead to significant fuel savings and improved overall efficiency.
3. Challenges in Material Properties and Quality Control
While 3D printing offers many advantages, it also presents several challenges, particularly in terms of material properties and quality control. The use of 3D printing requires careful selection of materials and processes to ensure that the resulting components meet the required specifications. Lockheed Martin has invested significant resources in developing and qualifying 3D printing materials and processes to ensure that the resulting components meet the required standards.

4. Integration with Traditional Manufacturing Methods
The use of 3D printing in aerospace engineering does not necessarily replace traditional manufacturing methods but rather complements them. Lockheed Martin has developed hybrid manufacturing approaches that combine 3D printing with traditional methods, such as machining and casting. This enables the creation of complex components that combine the benefits of both approaches.
5. Future Directions and Applications
The use of 3D printing in aerospace engineering is rapidly evolving, with new applications and technologies emerging continuously. Lockheed Martin is exploring the use of 3D printing for a range of applications, including satellite components, aircraft structures, and rocket engines. As the technology continues to mature, we can expect to see increased adoption of 3D printing in aerospace engineering, leading to improved performance, reduced costs, and new innovative applications.
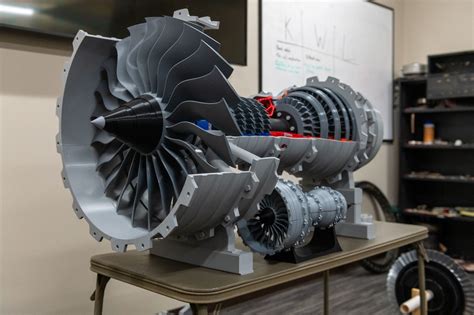
Gallery of 3D Printing Lockheed Engine
3D Printing Lockheed Engine Image Gallery
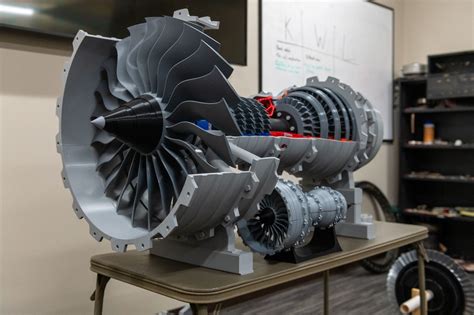
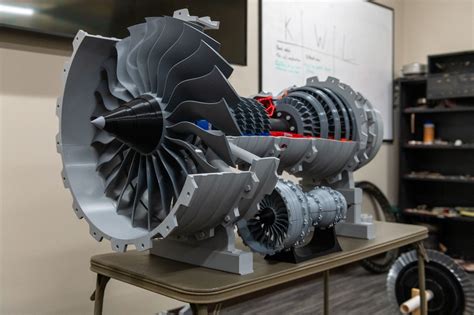

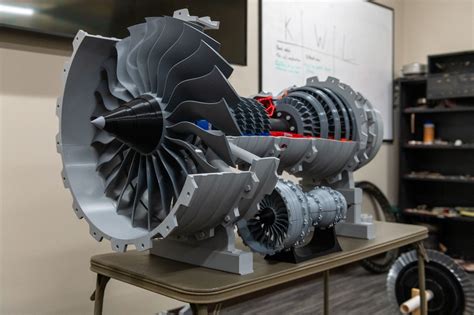
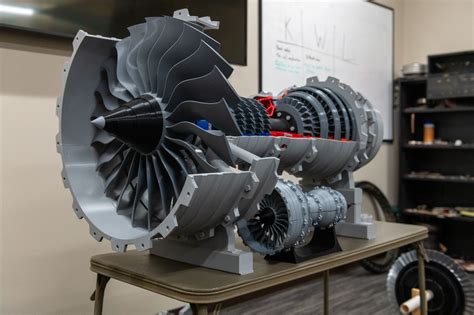
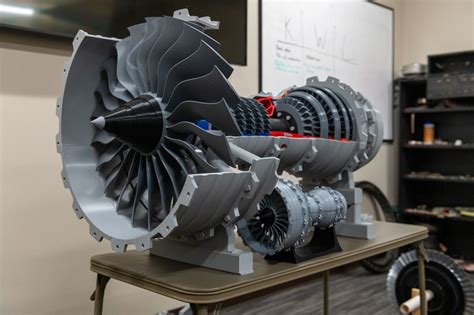
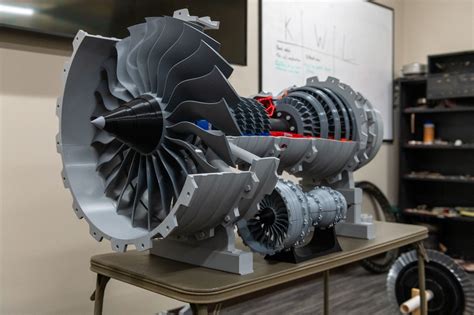
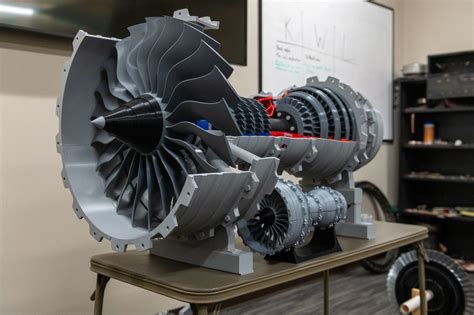
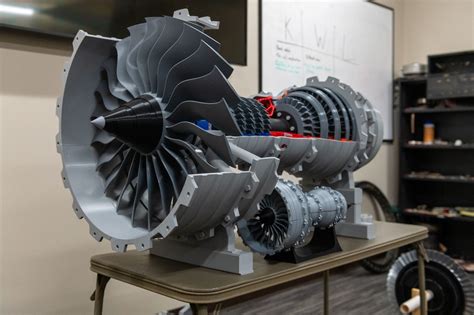
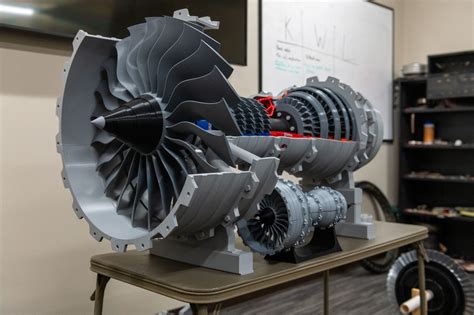
The use of 3D printing in aerospace engineering is a rapidly evolving field, with new applications and technologies emerging continuously. Lockheed Martin's adoption of 3D printing for engine components is a significant step forward, offering improved performance, reduced costs, and new innovative applications. As the technology continues to mature, we can expect to see increased adoption of 3D printing in aerospace engineering, leading to exciting new developments and innovations.
We hope this article has provided valuable insights into the world of 3D printing Lockheed engines. Share your thoughts and comments below, and let's continue the conversation!