Master the art of MIG welding stainless steel with these 5 expert techniques. Learn how to achieve strong, corrosion-resistant welds using MIG welding processes, including proper joint preparation, shielding gas selection, and temperature control. Discover the benefits of MIG welding stainless steel, including increased speed and efficiency.
MIG (GMAW) welding is a popular process for joining stainless steel due to its ease of use, high welding speeds, and good penetration. However, welding stainless steel can be challenging, and it requires careful preparation and technique to produce high-quality welds. Here are five ways to MIG weld stainless steel, along with some tips and best practices to help you achieve successful results.
Understanding Stainless Steel and MIG Welding
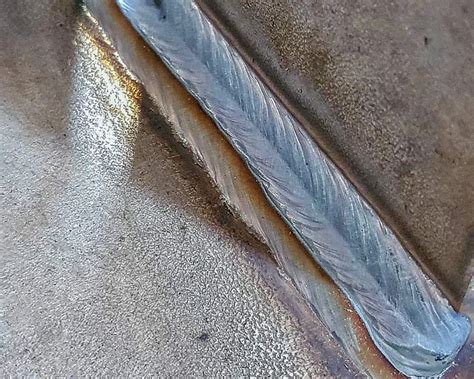
Before we dive into the specifics of MIG welding stainless steel, it's essential to understand the basics of both the material and the process. Stainless steel is a corrosion-resistant alloy that contains a minimum of 10.5% chromium content. It's widely used in various industries, including food processing, chemical, and pharmaceutical, due to its excellent corrosion resistance and durability.
MIG welding, also known as GMAW (Gas Metal Arc Welding), is a semi-automatic welding process that uses a continuous wire electrode and an inert gas to shield the arc. The process is well-suited for welding stainless steel due to its ability to produce high-quality welds with minimal distortion.
Choosing the Right Shielding Gas
When MIG welding stainless steel, it's crucial to choose the right shielding gas to protect the weld area from atmospheric gases, such as nitrogen and oxygen, which can cause porosity and lack of fusion. The most common shielding gases used for MIG welding stainless steel are:
- Argon (Ar)
- Helium (He)
- Argon-Helium mixtures (Ar-He)
- Argon-Carbon Dioxide mixtures (Ar-CO2)
The choice of shielding gas depends on the specific application, weld joint design, and desired weld penetration.
5 Ways to MIG Weld Stainless Steel
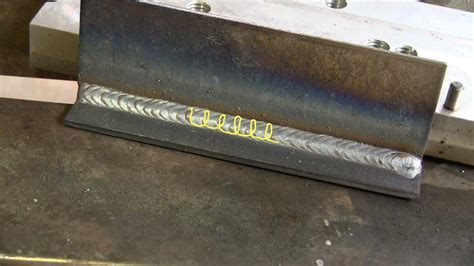
Here are five ways to MIG weld stainless steel, each with its unique characteristics and applications:
1. Short-Arc Welding
Short-arc welding is a low-energy process that uses a short arc length to produce a narrow, deep weld penetration. This process is ideal for welding thin-gauge stainless steel and is often used in applications where high accuracy and minimal distortion are critical.
2. Pulsed-Arc Welding
Pulsed-arc welding is a variation of short-arc welding that uses a pulsed current to create a series of high-energy arcs. This process produces a wider weld penetration than short-arc welding and is suitable for welding thicker stainless steel sections.
3. Spray-Arc Welding
Spray-arc welding is a high-energy process that uses a long arc length to produce a wide, shallow weld penetration. This process is ideal for welding thick stainless steel sections and is often used in applications where high welding speeds are required.
4. Globular-Arc Welding
Globular-arc welding is a variation of spray-arc welding that uses a lower voltage and a shorter arc length to produce a globular-shaped weld pool. This process is suitable for welding thin-gauge stainless steel and is often used in applications where high accuracy and minimal distortion are critical.
5. Buried-Arc Welding
Buried-arc welding is a process that uses a flux-cored wire to produce a weld pool that is shielded from the atmosphere. This process is ideal for welding stainless steel in applications where high weld penetration and minimal distortion are critical.
Best Practices for MIG Welding Stainless Steel
To achieve successful results when MIG welding stainless steel, follow these best practices:
- Cleanliness is crucial: Ensure that the weld area is clean and free of contamination, such as oil, grease, and moisture.
- Use the right shielding gas: Choose the right shielding gas for the specific application and weld joint design.
- Use a high-quality wire: Choose a high-quality wire that is specifically designed for MIG welding stainless steel.
- Maintain proper welding technique: Use a consistent welding technique, including welding speed, voltage, and wire feed speed.
- Monitor weld penetration: Monitor weld penetration to ensure that it meets the required specifications.
Tips and Tricks for MIG Welding Stainless Steel
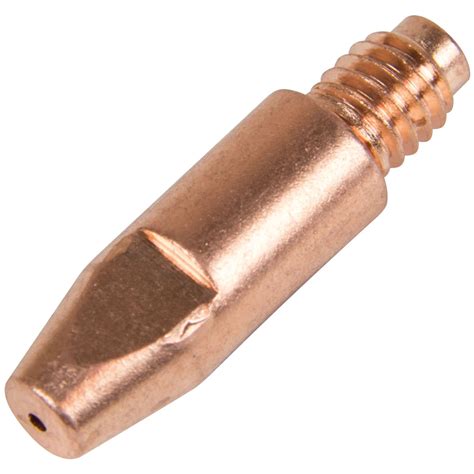
Here are some additional tips and tricks for MIG welding stainless steel:
- Use a push technique: Use a push technique to direct the weld pool and achieve a consistent weld penetration.
- Use a weaving pattern: Use a weaving pattern to maintain a consistent weld width and prevent lack of fusion.
- Monitor weld pool size: Monitor weld pool size to ensure that it is consistent and meets the required specifications.
- Use a heat sink: Use a heat sink to dissipate heat and prevent distortion.
Common Challenges and Solutions
Here are some common challenges and solutions when MIG welding stainless steel:
- Porosity: Use a higher shielding gas flow rate or adjust the welding technique to prevent porosity.
- Lack of fusion: Use a higher voltage or adjust the welding technique to achieve a consistent weld penetration.
- Distortion: Use a heat sink or adjust the welding technique to prevent distortion.
MIG Welding Stainless Steel Image Gallery
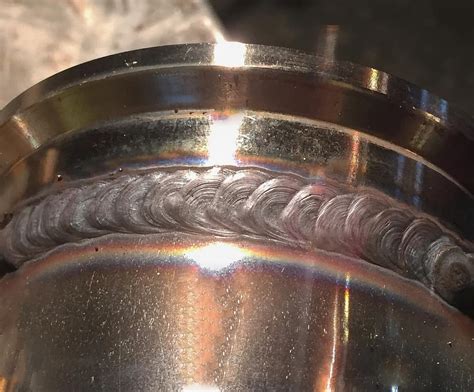
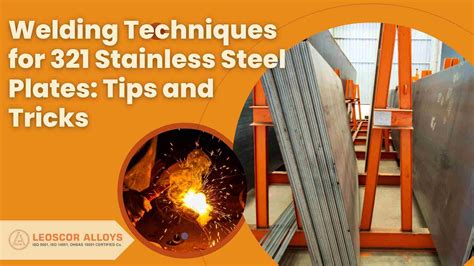
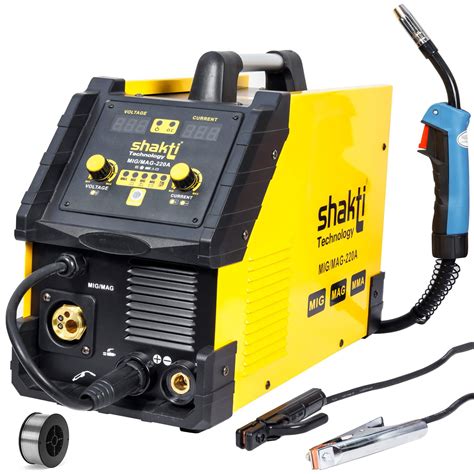
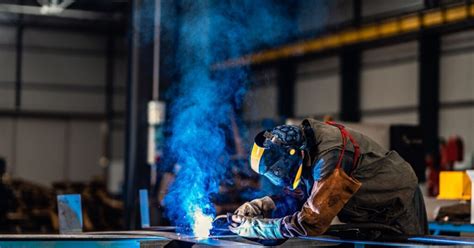
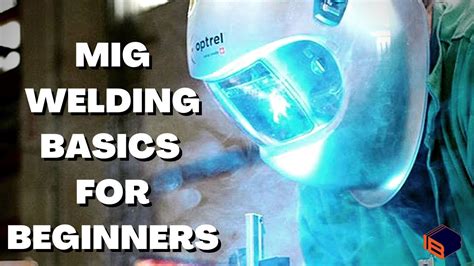
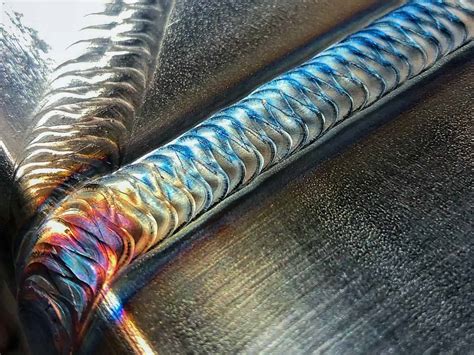
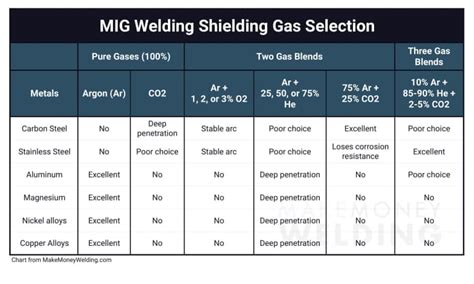
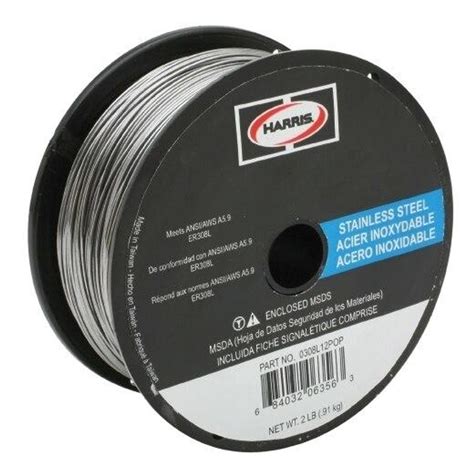
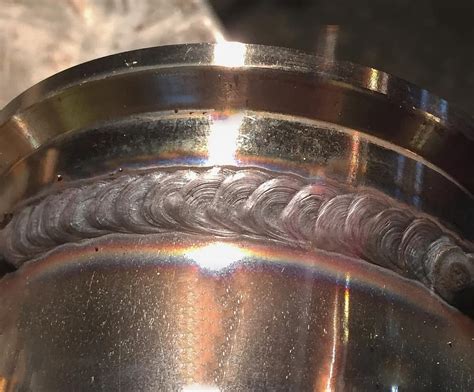
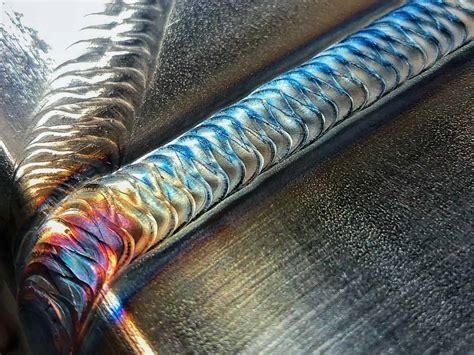
By following these tips and best practices, you can achieve successful results when MIG welding stainless steel. Remember to always use high-quality equipment, follow proper welding techniques, and monitor weld penetration to ensure that it meets the required specifications.
If you have any questions or comments, please feel free to share them below.