Discover the hidden dangers of faulty welds in shipyard safety. Learn how defective welds can lead to catastrophic failures, equipment damage, and even loss of life in Newport News shipyards. Explore 5 critical ways faulty welds impact safety, including structural integrity, corrosion, and regulatory non-compliance, and understand the importance of quality welding practices.
The importance of ensuring the integrity of welds in shipbuilding cannot be overstated. Faulty welds can have a ripple effect, impacting not only the structural integrity of the vessel but also the safety of those who work on and around it. In a shipyard like Newport News, where some of the world's most advanced warships are built, the stakes are high. A single faulty weld can lead to catastrophic consequences, putting the lives of thousands of sailors and shipbuilders at risk.
In the high-stakes world of shipbuilding, attention to detail is crucial. Welders, engineers, and quality control specialists must work together to ensure that every weld meets the highest standards. However, even with the best intentions and most stringent quality control measures in place, mistakes can happen. When they do, the consequences can be severe.
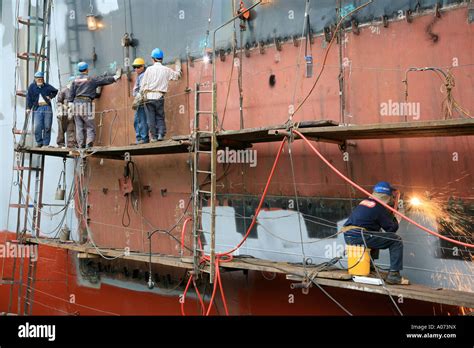
How Faulty Welds Impact Shipyard Safety in Newport News
Faulty welds can have a significant impact on shipyard safety in Newport News. Here are five ways in which a faulty weld can put people and vessels at risk:
1. Structural Integrity
A faulty weld can compromise the structural integrity of a vessel, making it more susceptible to damage or failure. This can be particularly problematic in a shipyard like Newport News, where vessels are built to withstand the harsh conditions of the open ocean. If a weld fails, the consequences can be catastrophic, leading to costly repairs, injuries, or even loss of life.
2. Fire Hazards
Faulty welds can also create fire hazards, particularly in areas where flammable materials are present. A spark or electrical arc can ignite nearby fuels, leading to a devastating fire that can spread quickly throughout the shipyard. In a shipyard like Newport News, where welding and cutting operations are common, the risk of fire is ever-present.
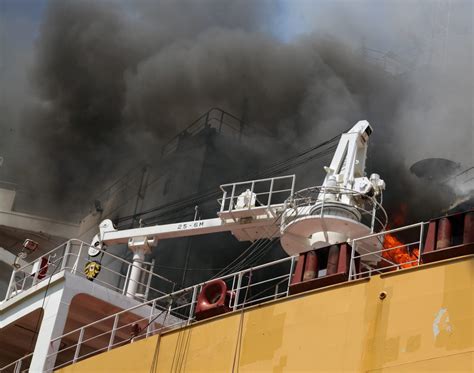
3. Electrical Shock
Faulty welds can also create electrical shock hazards, particularly in areas where electrical equipment is present. A faulty weld can create a path for electrical current to flow, leading to a shock or even electrocution. In a shipyard like Newport News, where electrical systems are complex and widespread, the risk of electrical shock is a serious concern.
4. Environmental Hazards
Faulty welds can also create environmental hazards, particularly in areas where hazardous materials are present. A faulty weld can release toxic chemicals or fuels into the environment, posing a risk to both human health and the ecosystem. In a shipyard like Newport News, where environmental regulations are strict, the consequences of a faulty weld can be severe.
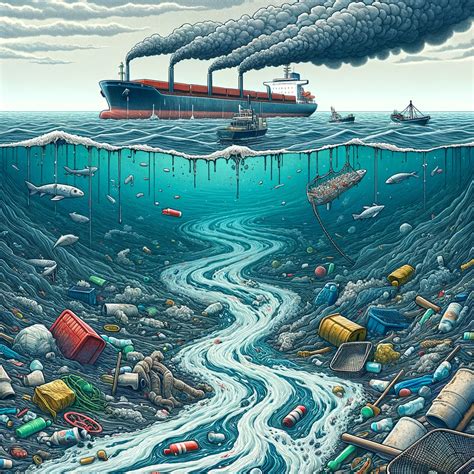
5. Economic Consequences
Finally, faulty welds can have significant economic consequences, both for the shipyard and the vessel's owner. A faulty weld can lead to costly repairs, delays, and even loss of business. In a competitive industry like shipbuilding, the consequences of a faulty weld can be severe, impacting not only the shipyard's reputation but also its bottom line.
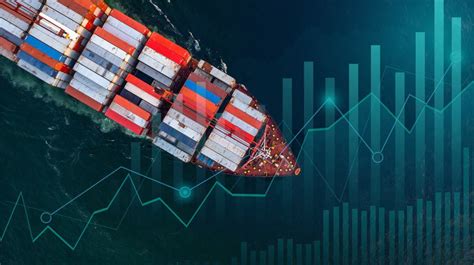
Preventing Faulty Welds in Shipbuilding
Preventing faulty welds requires a multi-faceted approach that involves everyone from welders to engineers to quality control specialists. Here are some strategies for preventing faulty welds in shipbuilding:
1. Proper Training
Proper training is essential for welders, engineers, and quality control specialists. This includes training in welding techniques, safety protocols, and quality control procedures. By investing in training, shipyards can ensure that their employees have the skills and knowledge they need to produce high-quality welds.
2. Quality Control Procedures
Quality control procedures are critical for preventing faulty welds. This includes regular inspections, testing, and certification of welds. By implementing robust quality control procedures, shipyards can ensure that every weld meets the highest standards.
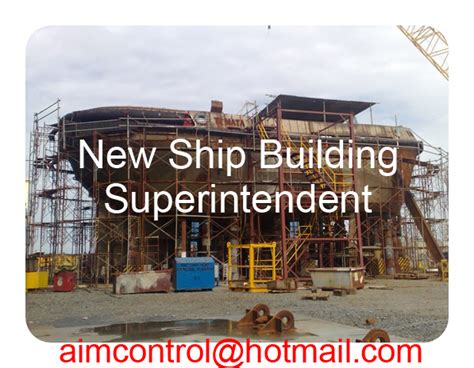
3. Equipment Maintenance
Equipment maintenance is also essential for preventing faulty welds. This includes regular maintenance of welding equipment, electrical systems, and other critical infrastructure. By keeping equipment in good working order, shipyards can reduce the risk of faulty welds.
4. Safety Protocols
Safety protocols are critical for preventing faulty welds. This includes protocols for fire prevention, electrical safety, and environmental protection. By implementing robust safety protocols, shipyards can reduce the risk of accidents and injuries.
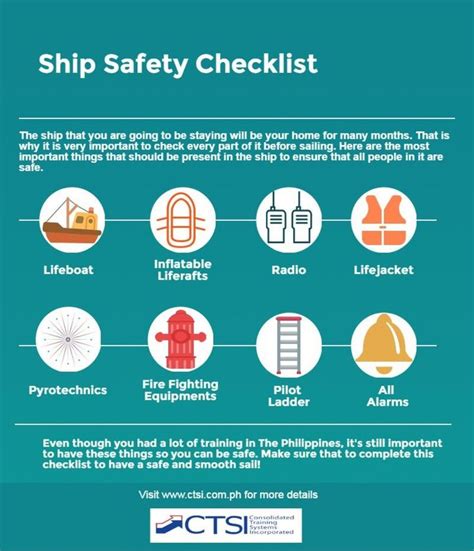
Conclusion
Faulty welds can have a significant impact on shipyard safety in Newport News, compromising structural integrity, creating fire hazards, electrical shock hazards, environmental hazards, and economic consequences. By investing in proper training, quality control procedures, equipment maintenance, and safety protocols, shipyards can reduce the risk of faulty welds and ensure the highest standards of safety and quality.
Now it's your turn. Share your thoughts on the importance of preventing faulty welds in shipbuilding. What strategies do you think are most effective for preventing faulty welds? Share your comments below.
Shipbuilding Safety Image Gallery

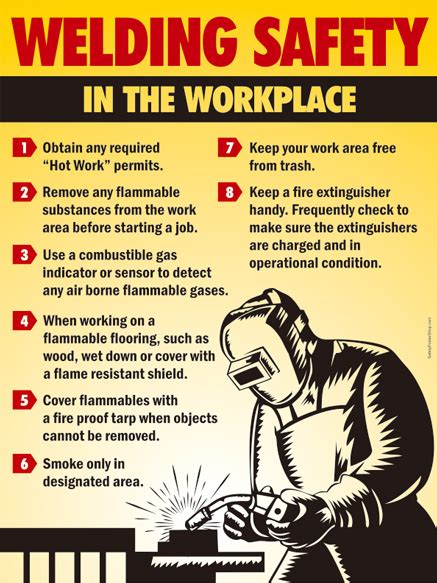
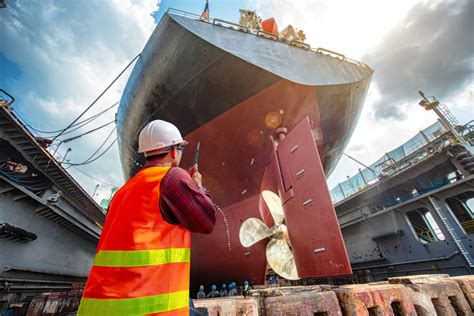

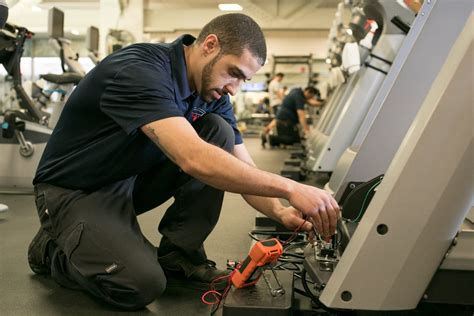
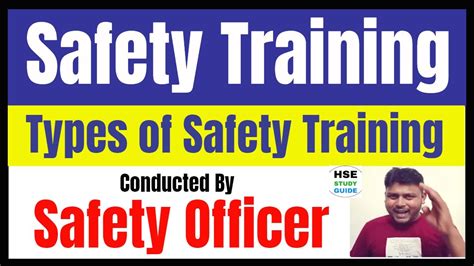
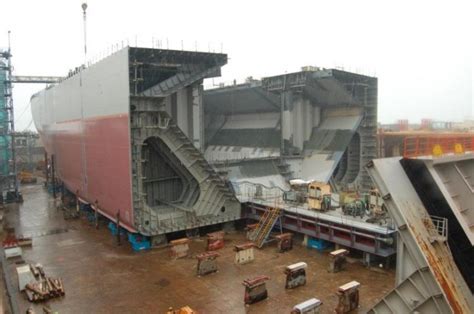
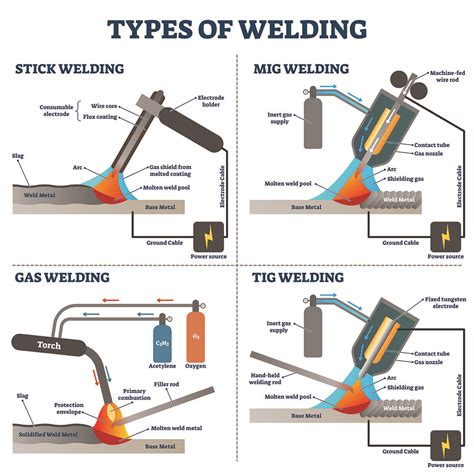
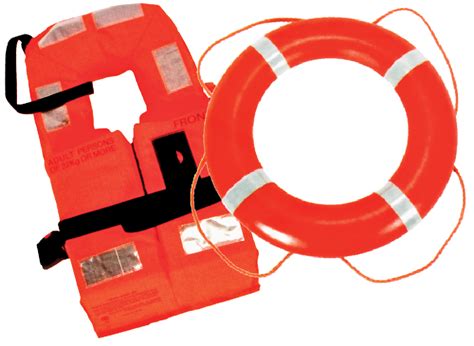
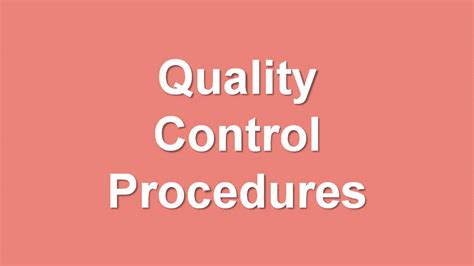