Intro
When it comes to managing the costs of formulas, whether for business or personal use, understanding the expenses involved is crucial for effective budgeting and financial planning. Calculating the formula cost for a year can be complex, depending on the type of formula and its application. However, there are several methods and strategies that can simplify this process. In this article, we will explore five practical ways to calculate the formula cost for a year, encompassing various scenarios and formula types.
The Importance of Accurate Formula Costing
Before diving into the methods, it's essential to understand why accurate formula costing is important. For businesses, incorrect costing can lead to under or overpricing of products, affecting profit margins and competitiveness. For individuals, especially those in research or development, accurate costing helps in managing resources efficiently and securing funding. With the right approach, one can navigate the complexities of formula costs effectively.
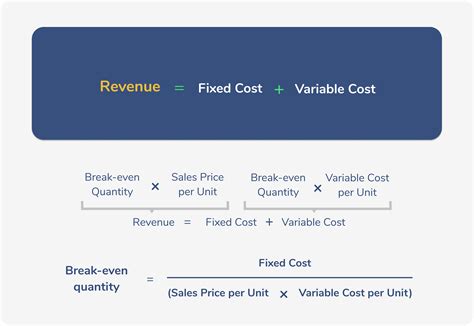
1. Material Quantity and Cost Method
This method involves calculating the cost of the formula based on the quantity of materials required for its preparation. It's especially useful for chemical or pharmaceutical formulas where the cost of raw materials can significantly impact the overall cost.
- Step 1: Identify all the materials needed for the formula and their respective quantities for one unit of the formula.
- Step 2: Determine the cost of each material based on the current market rate or supplier quotes.
- Step 3: Multiply the quantity of each material by its cost to get the total cost of materials for one unit of the formula.
- Step 4: Multiply the cost of one unit of the formula by the number of units needed for a year.
Example: A formula requires 2kg of Material A ($10/kg) and 1kg of Material B ($5/kg) to make one unit. For 100 units, the calculation would be: (2kg * $10/kg) + (1kg * $5/kg) = $30 per unit. For 100 units, the total cost would be 100 units * $30/unit = $3000.
2. Labor and Overhead Method
This method is crucial for formulas that involve significant labor or overhead costs, such as manufacturing processes requiring specialized equipment or skilled labor.
- Step 1: Calculate the labor cost per unit of the formula based on the time and expertise required.
- Step 2: Determine the overhead costs, including equipment depreciation, utilities, and facility costs.
- Step 3: Add the labor and overhead costs to the material cost calculated using the first method to get the total cost per unit.
- Step 4: Multiply the total cost per unit by the number of units required for a year.
Example: If the labor cost per unit is $20 and the overhead cost is $10, the total cost per unit would be $30 (material cost) + $20 (labor) + $10 (overhead) = $60 per unit.
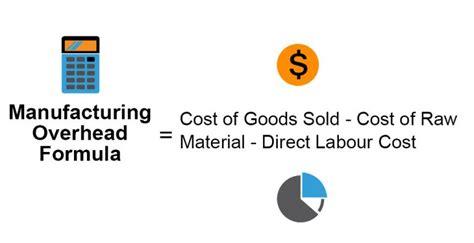
3. Market Research Method
This method involves researching the market to determine the average cost of similar formulas or products. It's useful for businesses looking to price their products competitively.
- Step 1: Identify similar formulas or products in the market.
- Step 2: Research their prices, considering any discounts or promotions.
- Step 3: Calculate the average price of these similar products.
- Step 4: Adjust the average price based on your formula's unique features, quality, or brand value.
Example: If similar products are priced between $50 to $70 per unit, the average price would be around $60. However, if your product has a unique feature that adds value, you might price it slightly higher, at $65 per unit.
4. Life Cycle Costing Method
This method considers all costs associated with the formula throughout its life cycle, from development to disposal. It's particularly useful for long-term projects or formulas with significant maintenance or disposal costs.
- Step 1: Identify all costs associated with the formula, including development, production, maintenance, and disposal.
- Step 2: Calculate these costs over the life cycle of the formula.
- Step 3: Determine the annual cost by dividing the total life cycle cost by the number of years the formula will be in use.
Example: If the total life cycle cost of a formula is $100,000 over 5 years, the annual cost would be $20,000 per year.
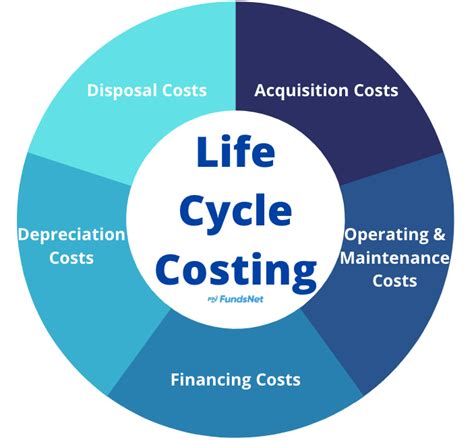
5. Activity-Based Costing (ABC) Method
This method involves assigning costs to activities or tasks involved in producing the formula, rather than just materials or labor. It's useful for complex formulas with multiple processes.
- Step 1: Identify all activities involved in producing the formula.
- Step 2: Calculate the cost of each activity.
- Step 3: Assign these costs to the formula based on the activities used.
- Step 4: Calculate the total cost per unit of the formula.
Example: If Activity A costs $10 per unit and Activity B costs $5 per unit, and both are required for one unit of the formula, the total cost per unit would be $15.
Gallery of Formula Cost Calculations
Formula Cost Calculations Gallery
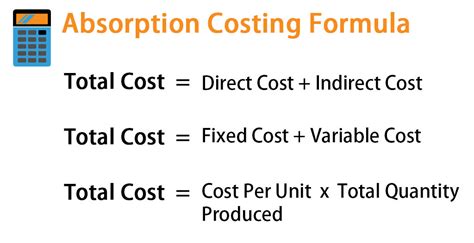
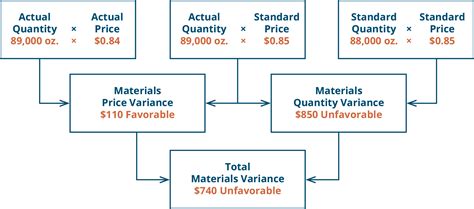
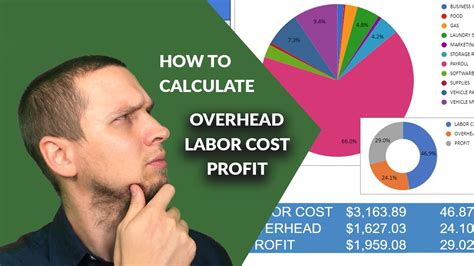
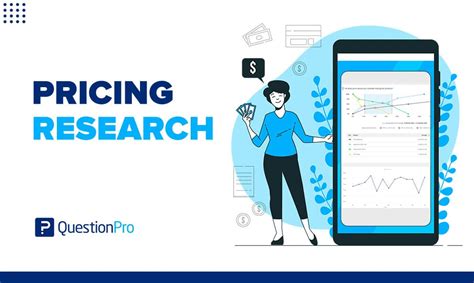
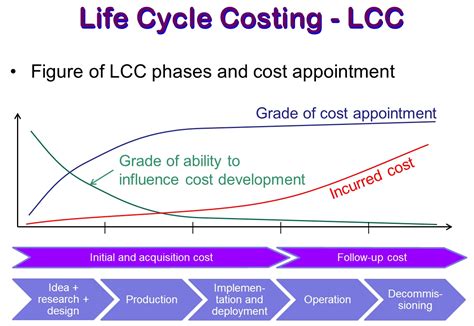
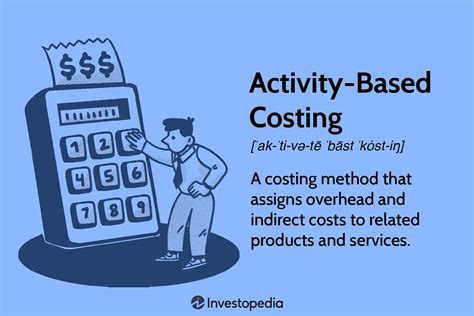
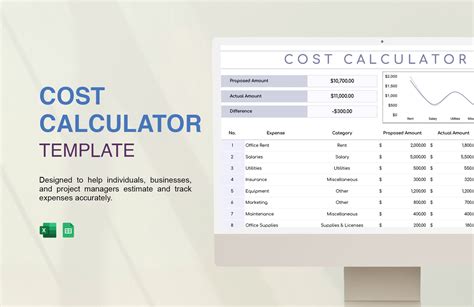
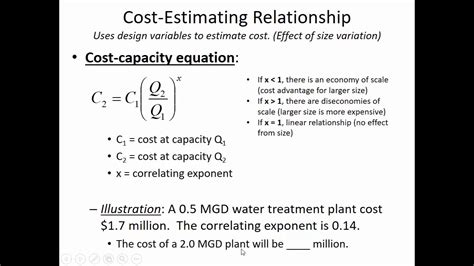

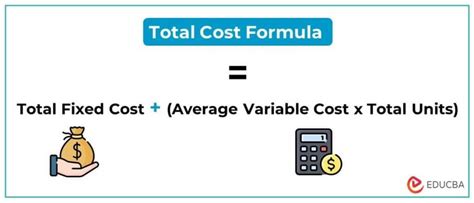
Conclusion: Calculating the Right Cost
Calculating the formula cost for a year involves more than just adding up the costs of materials and labor. It requires understanding the complexities of the formula, the market, and the activities involved in its production. By using one or a combination of the methods outlined above, individuals and businesses can accurately determine the cost of their formulas, making informed decisions that impact profitability and competitiveness. Whether you're in the initial stages of product development or looking to optimize existing processes, understanding formula costs is key to success in today's fast-paced and competitive market.
Share Your Thoughts
Have you used any of these methods to calculate formula costs? Share your experiences and insights in the comments below. Also, don't forget to share this article with others who might find it helpful.