Intro
Ensuring the safety of workers and maintaining compliance with regulatory standards is crucial for any organization that operates with machinery or equipment. One critical aspect of achieving this goal is implementing a comprehensive Lockout Tagout (LOTO) procedure. LOTO is a process used to prevent accidental startup of machinery or equipment during maintenance, servicing, or when not in use, thereby protecting employees from injuries and fatalities.
Why Is Lockout Tagout Procedure Important?
The importance of having a Lockout Tagout procedure in place cannot be overstated. It serves as a crucial safeguard for employees who perform maintenance tasks on equipment, ensuring that the machine is completely de-energized and safe to work on. Moreover, it aids organizations in complying with OSHA standards (Occupational Safety and Health Administration) in the United States, as well as similar regulatory bodies in other countries, which mandate such procedures to prevent workplace injuries and fatalities.
Key Elements of a Lockout Tagout Procedure
Implementing an effective LOTO procedure involves several key elements:
- Policy: A clear company policy stating the importance of LOTO and the commitment to its implementation.
- Procedure: Detailed steps outlining how to properly lock out or tag out equipment, including how to shut off, dissipate, and secure energy sources.
- Training: Regular training sessions for all employees involved in the LOTO process to ensure they understand their roles and responsibilities.
- Responsibilities: Clearly defined roles for each individual involved in the LOTO process, including the authorized employee who performs the lockout/tagout, the affected employees who may be impacted by the lockout/tagout, and supervisors who oversee the process.
- Equipment-Specific Procedures: Since different equipment may have unique shutdown procedures, it's essential to have equipment-specific procedures that detail the steps for each piece of machinery.
Creating a Lockout Tagout Procedure Template in Excel
Using Excel to create a LOTO procedure template can help organize and streamline the process. Here’s a basic outline of what such a template might include:
Lockout Tagout Procedure Template in Excel

1. Introduction
- Purpose: A brief overview of the purpose of the LOTO procedure.
- Scope: Who the procedure applies to.
- Responsibilities: Roles and responsibilities of individuals involved.
2. General Procedure
- Preparation: Steps to prepare for lockout/tagout, including notifying affected employees.
- Shutdown: Detailed steps for shutting down the equipment.
- Lockout/Tagout: Procedures for applying locks and tags.
- Verification: Steps for verifying that the equipment is safely de-energized.
3. Equipment-Specific Procedures
- A list or table detailing specific procedures for each piece of equipment, including shutdown steps, energy sources to lock out/tag out, and any special considerations.
4. Training and Enforcement
- Training Requirements: Details on training for employees involved in the LOTO process.
- Enforcement: Actions to be taken for non-compliance.
5. Review and Revision
- A section outlining the schedule for reviewing and revising the LOTO procedure to ensure it remains effective and compliant with regulatory standards.
Implementing and Reviewing the LOTO Procedure
Implementing a LOTO procedure is not a one-time task; it requires continuous monitoring and revision. Regular audits and reviews of the procedure are essential to ensure it remains effective and compliant with regulatory standards. Moreover, feedback from employees who use the procedure can provide valuable insights into how it can be improved.
Conclusion
A well-designed Lockout Tagout procedure is a critical component of any workplace safety program. By using an Excel template to create and manage this procedure, organizations can ensure that their LOTO process is clear, comprehensive, and easily accessible to all employees. Remember, the safety of your workforce depends on it.
Lockout Tagout Procedure Template in Excel Image Gallery
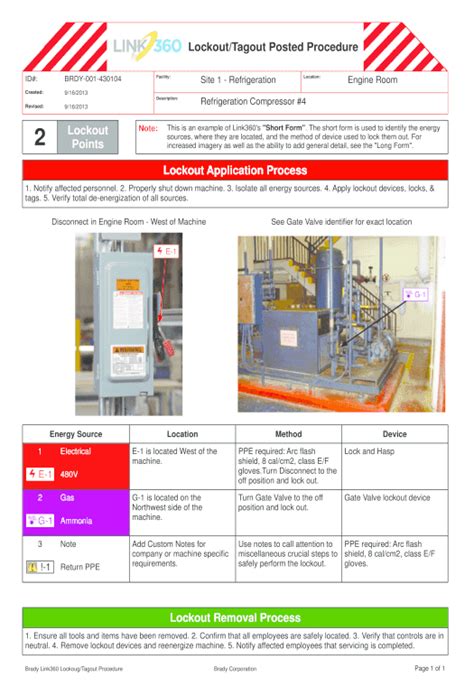
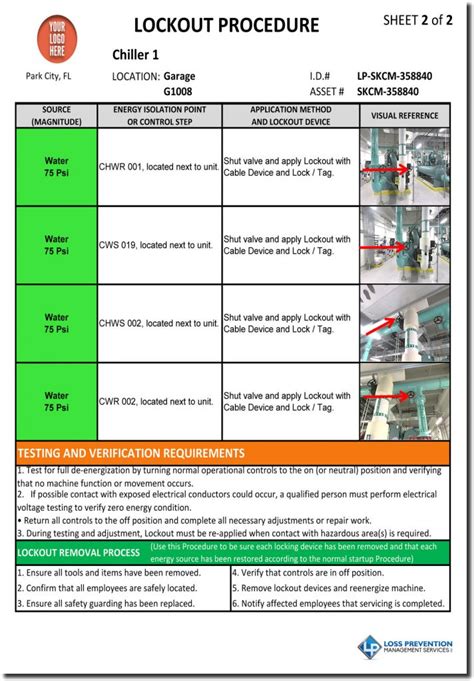
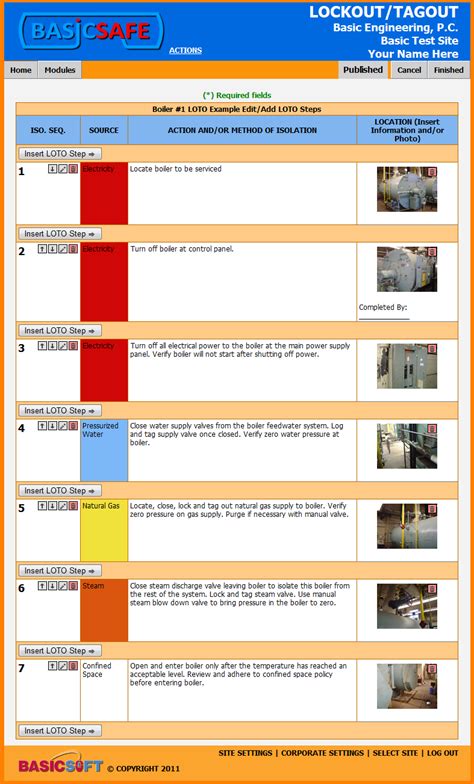
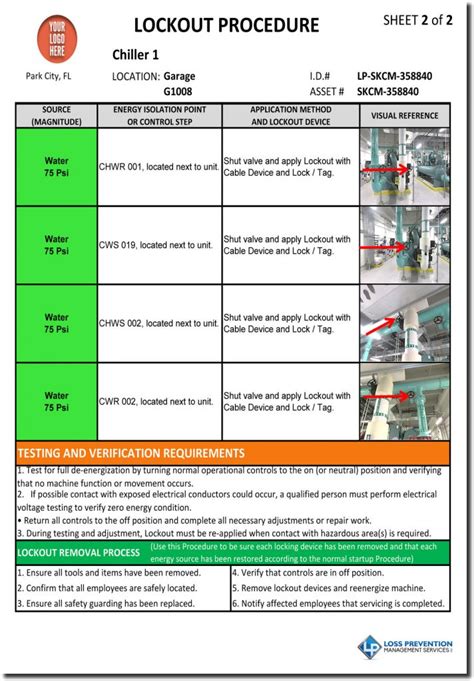
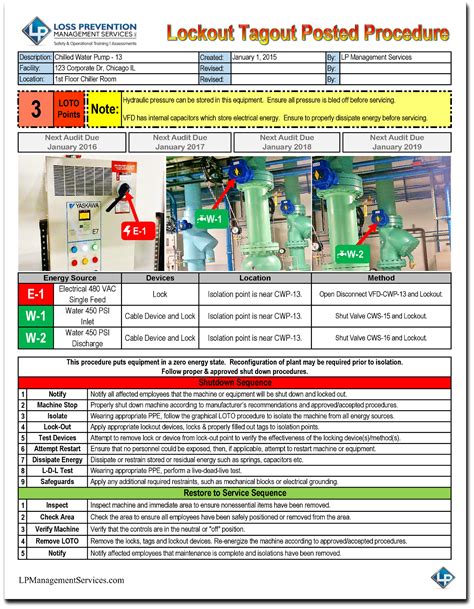
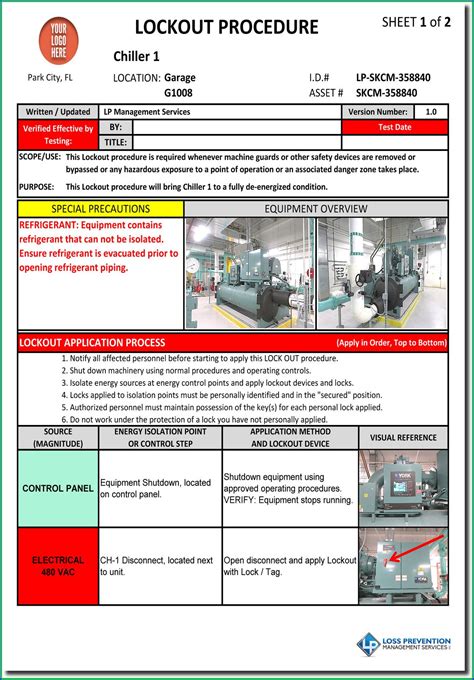
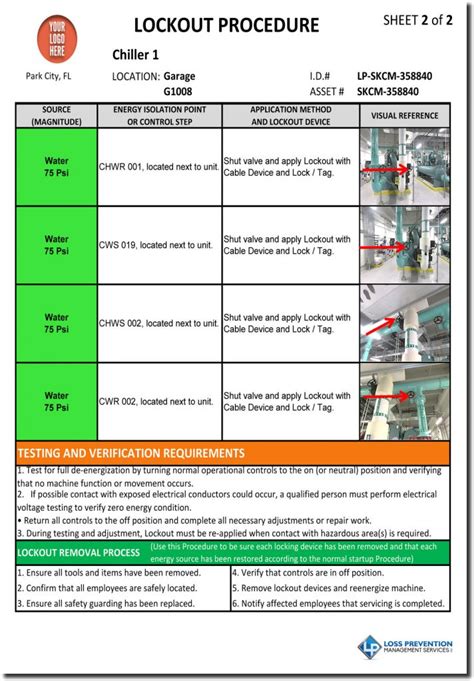
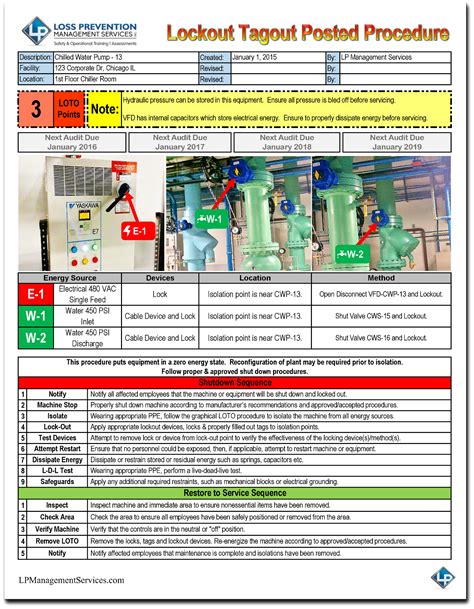
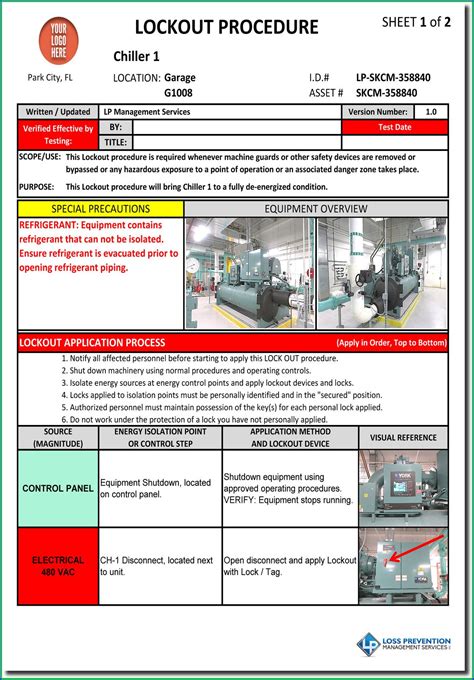
