Intro
Conduct a thorough workplace safety inspection with our comprehensive checklist. Ensure a hazard-free environment by identifying potential risks and implementing corrective measures. Our 10 essential items checklist covers crucial areas such as fire safety, ergonomics, fall protection, and electrical safety, helping you maintain compliance and prevent workplace accidents.
Maintaining a safe working environment is crucial for the well-being of employees and the overall success of a business. A workplace safety inspection is an essential tool to identify potential hazards and take corrective action to prevent accidents and injuries. In this article, we will provide you with a comprehensive guide to creating an effective workplace safety inspection checklist.
Why Workplace Safety Inspections are Important
Workplace safety inspections are a vital component of a company's health and safety management system. These inspections help to identify potential hazards, assess risks, and implement control measures to prevent accidents and injuries. Regular safety inspections can also help to reduce the risk of workplace fatalities, injuries, and illnesses.
Benefits of a Workplace Safety Inspection Checklist
A workplace safety inspection checklist is a valuable tool that helps to ensure a thorough and systematic inspection of the workplace. The benefits of using a safety inspection checklist include:
- Identifying potential hazards and risks
- Implementing control measures to prevent accidents and injuries
- Reducing the risk of workplace fatalities, injuries, and illnesses
- Improving employee morale and productivity
- Enhancing the company's reputation and image
- Reducing the risk of lawsuits and fines
10 Essential Items for a Workplace Safety Inspection Checklist
Here are 10 essential items to include in your workplace safety inspection checklist:
1. Hazardous Materials and Chemicals
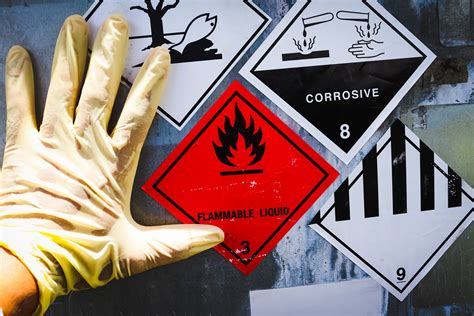
- Are hazardous materials and chemicals properly labeled and stored?
- Are employees trained on the safe handling and use of hazardous materials and chemicals?
- Are personal protective equipment (PPE) and emergency equipment available?
Sub-items:
- Check for proper ventilation and exhaust systems
- Verify that employees are wearing PPE when handling hazardous materials and chemicals
- Review material safety data sheets (MSDS) for each hazardous material and chemical
2. Electrical Safety
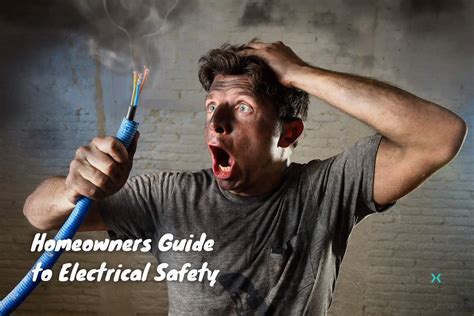
- Are electrical systems and equipment properly installed and maintained?
- Are employees trained on electrical safety procedures?
- Are electrical cords and cables properly secured and protected?
Sub-items:
- Check for frayed or damaged electrical cords and cables
- Verify that electrical equipment is properly grounded
- Review electrical safety procedures and protocols
3. Fire Safety
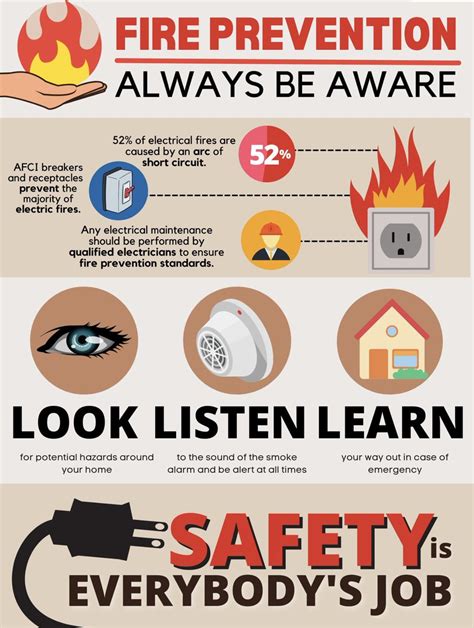
- Are fire extinguishers and fire suppression systems properly installed and maintained?
- Are employees trained on fire safety procedures?
- Are emergency exit routes and doors properly marked and maintained?
Sub-items:
- Check for proper fire extinguisher inspections and maintenance
- Verify that employees are trained on fire safety procedures and protocols
- Review emergency evacuation procedures
4. Fall Protection
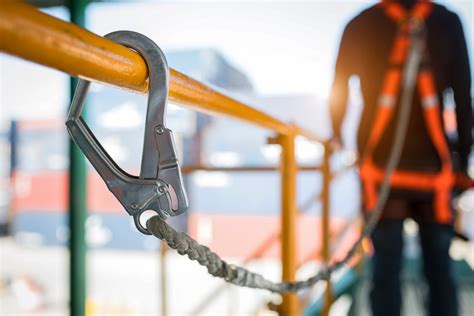
- Are fall protection systems and equipment properly installed and maintained?
- Are employees trained on fall protection procedures?
- Are guardrails and handrails properly installed and maintained?
Sub-items:
- Check for proper fall protection equipment inspections and maintenance
- Verify that employees are trained on fall protection procedures and protocols
- Review fall protection systems and equipment
5. Ergonomics and Musculoskeletal Disorders
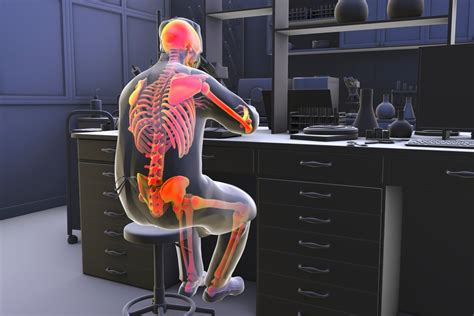
- Are workstations and work areas properly designed and maintained to prevent musculoskeletal disorders?
- Are employees trained on ergonomics and musculoskeletal disorder prevention procedures?
- Are employees encouraged to report musculoskeletal disorders and injuries?
Sub-items:
- Check for proper workstation and work area design
- Verify that employees are trained on ergonomics and musculoskeletal disorder prevention procedures
- Review musculoskeletal disorder prevention procedures and protocols
6. Personal Protective Equipment (PPE)
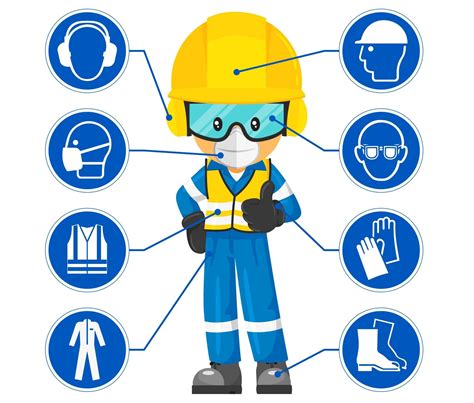
- Is PPE properly provided and maintained?
- Are employees trained on PPE use and maintenance procedures?
- Are employees required to wear PPE when necessary?
Sub-items:
- Check for proper PPE inspections and maintenance
- Verify that employees are trained on PPE use and maintenance procedures
- Review PPE use and maintenance procedures and protocols
7. Lockout/Tagout Procedures
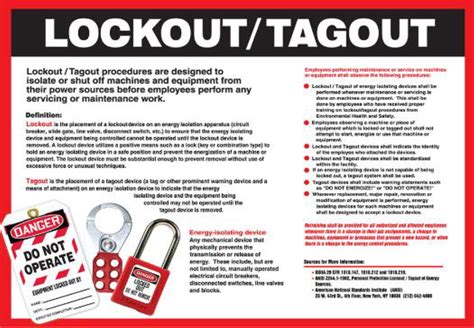
- Are lockout/tagout procedures properly implemented and maintained?
- Are employees trained on lockout/tagout procedures?
- Are lockout/tagout devices properly installed and maintained?
Sub-items:
- Check for proper lockout/tagout procedure inspections and maintenance
- Verify that employees are trained on lockout/tagout procedures
- Review lockout/tagout procedures and protocols
8. Hazard Reporting and Communication
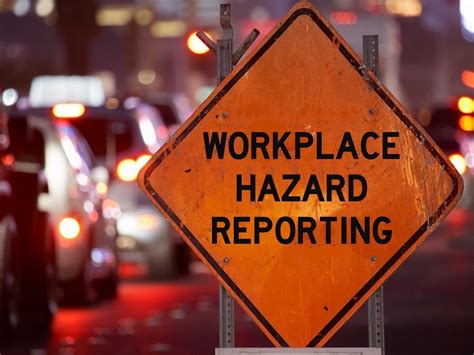
- Are employees encouraged to report hazards and near-miss incidents?
- Are hazard reports properly investigated and documented?
- Are employees informed of hazard reports and incident investigations?
Sub-items:
- Check for proper hazard reporting procedures
- Verify that employees are encouraged to report hazards and near-miss incidents
- Review hazard reporting and communication procedures and protocols
9. Emergency Preparedness and Response
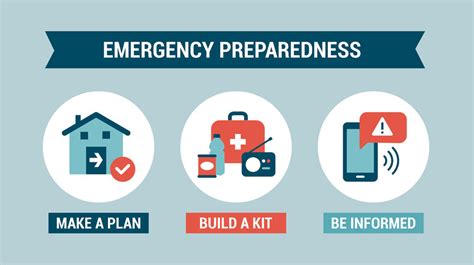
- Are emergency procedures properly implemented and maintained?
- Are employees trained on emergency response procedures?
- Are emergency equipment and supplies properly maintained and available?
Sub-items:
- Check for proper emergency procedure inspections and maintenance
- Verify that employees are trained on emergency response procedures
- Review emergency preparedness and response procedures and protocols
10. Training and Education
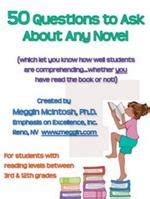
- Are employees properly trained on workplace safety procedures and protocols?
- Are employees provided with regular training and education on workplace safety topics?
- Are training records properly maintained and documented?
Sub-items:
- Check for proper training procedures and protocols
- Verify that employees are provided with regular training and education on workplace safety topics
- Review training records and documentation
Gallery of Workplace Safety Images
Workplace Safety Image Gallery

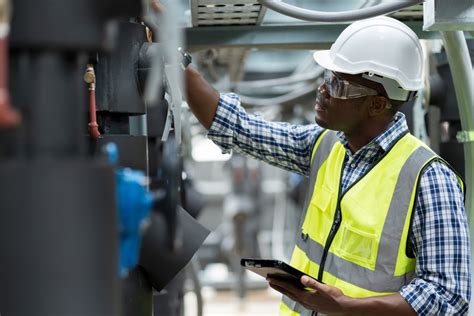
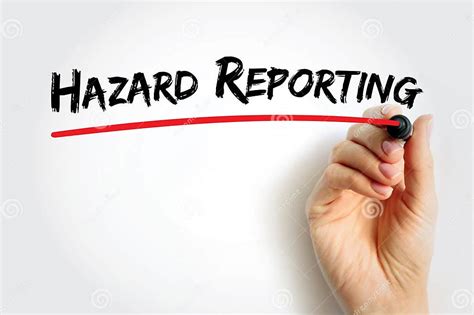
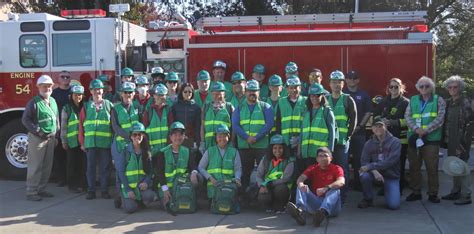
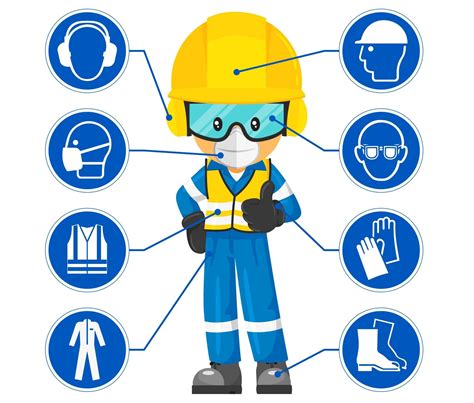
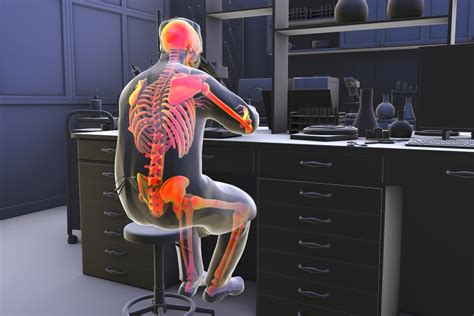
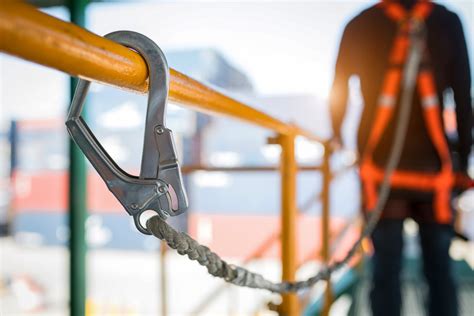
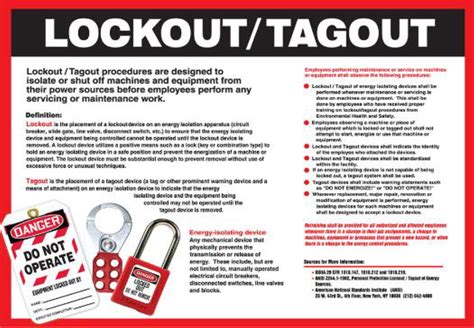
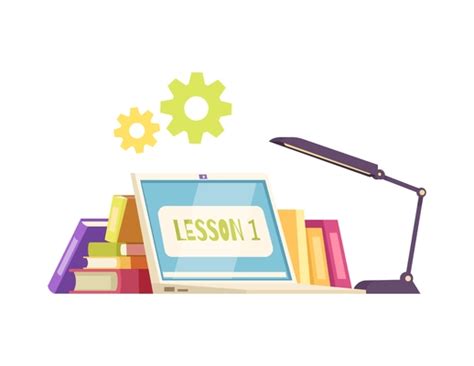
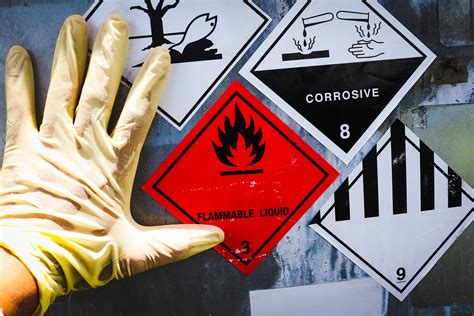
Conclusion
Creating an effective workplace safety inspection checklist is essential for maintaining a safe working environment. By including the 10 essential items outlined in this article, you can help to identify potential hazards, assess risks, and implement control measures to prevent accidents and injuries. Remember to regularly review and update your safety inspection checklist to ensure it remains relevant and effective.